Ribblesdale Cement Kiln
Ribblesdale Cement Kiln | |
![]() See Cement Kilns → page for a larger UK Wide map. | |
Waste Licence | BL7272IB |
Operator | Hanson Cement |
Parent Company | Heidelberg Cement Group |
Clinker Capacity | 0.75 Mt |
Summary site information collated from a variety of sources.
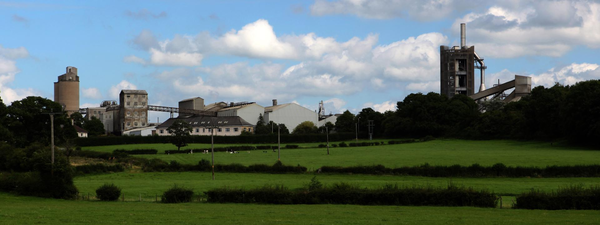
Overview
WikiWaste has used the website Cement Plants and Kilns in Britain and Ireland[1] extensively for the reference material for each individual cement kiln page. The detail on this reference website is extensive and as WikiWaste is focused upon the UK waste and resource market, only the key highlights are captured from this website (and company websites accordingly) to provide background and context. Ribblesdale started manufacturing clinker in 1936 and up to 2015 had produced 55 million tonnes of clinker through 7 rotary kilns over this period.
Ownership
- 1936 to 1986 Ribblesdale Cement Ltd (50% owned by Tunnel, 50% by Thomas W Ward to 1981, then by Rio Tino Zinc (RTZ))
- 1986 to 2009 Castle cement Ltd (RTZ to 1989, Scancem to 1999, HeidlebergCement to 2009)
- 2009 to Present Hanson Cement UK (owned by HeidelbergCement)
The Process at Ribblesdale
The process at the site is an air-separated precalciner kiln, supplied by FLS (FLSmidth) which allows for the burning of alternative fuels[2].
Raw Materials
The primary raw materials are Carboniferous Limestone from the adjacent quarry, using interlaced shale on the same site and superficial clay.
Waste Used on Site
The Ribblesdale site waste return to the EA for the most recent year of 2018 showed 153,269 tonnes of the following wastes used on site:
Waste Class | Description | Tonnage Input |
---|---|---|
02 02 03 | materials unsuitable for consumption or processing | 890 |
06 02 01* | calcium hydroxide | 1,128 |
10 01 02 | coal fly ash | 66,800 |
16 08 04 | spent fluid catalytic cracking catalysts (except 16 08 07) | 2,376 |
19 02 08* | liquid combustible wastes containing dangerous substances | 19,587 |
19 08 13* | sludges containing dangerous substances from other treatment of industrial waste water | 2,875 |
19 12 10 | combustible waste (refuse derived fuel) | 52,557 |
19 12 11* | other wastes (including mixtures of materials) from mechanical treatment of waste containing dangerous substances | 745 |
19 12 12 | other wastes (including mixtures of materials) from mechanical treatment of wastes other than those mentioned in 19 12 11 | 950 |
Just under 40% of the tonnage listed for the primary purpose of substituting fuel requirements in the plant, with 55% of coal fly ash (also called Pulverized Fuel Ash or PFA) used in as a replacement for raw material in the production process. The most recent annual performance report from 2016 did not report the exact tonnage used - quoting commercial confidentiality[3].