Gas Fermentation
Gas Fermentation is the production of fuels from biomass by the use of microorganisms. Biomass is gasified to a mixture of carbon monoxide (CO), carbon dioxide (CO2), hydrogen (H2), and nitrogen (N2), known as the synthesis gas or syngas[1]. The microorganisms then fix the available carbon contained within the biomass into platform chemicals, fuels and polymers[2]. This is achieved via the Wood-Ljungdahl Pathway (WLP) which is the most efficient known pathway to convert CO2 to secreted organic products[3].
The Process
Gas fermentation can be divided into four steps:
- Generation of syngas
- Gas pre-treatment
- Gas fermentation in a bioreactor
- Product separation
Generation of syngas
The biomass is gasified which results in the carbonaceous material reacting with steam and air at elevated temperature (600-1000°C) and high pressure (>30 bar) to form a syngas or synthetic gas of variable composition. Excess heat generated from gasification can be used to generate steam for product distillation and/or electricity.
Gas Pre-treatment
As well as the main constituents (CO, H2, CO2), input gas streams can also contain impurities such as particulates, tar and aromatics and other inhibiting gases which need to be removed in order for the microorganisms to operate efficiently. Particulates can be removed by cyclone separators and filters. Tars can be condensed and removed by quenching hot syngas or alternatively can be reformed by heating at 800-900 °C using olivine, dolomite and nickel compounds as catalysts, producing additional syngas.
Gas Fermentation
The treated syngas is cooled and compressed and then sparged into a bioreactor containing the gas-fermenting microorganisms in an aqueous medium. There is a multitude of variables to consider to ensure the yield of the desired product such as bioreactor design, agitation, gas composition and supply rate, pH, temperature, headspace pressure, oxidation-reduction potential (ORP), nutrients and amount of foaming in the bioreactor.
Product Separation
The final stage is required to separate the desired metabolic product from the fermentation broth. Technologies that help achieve this are distillation systems, liquid-liquid extraction, gas stripping, absorption, perstraction, pervaporation and vacuum distillation[2].
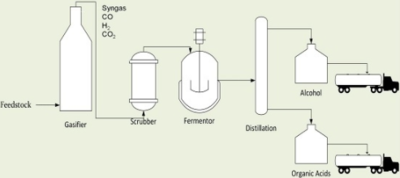