Ballistic Separator
A Ballistic Separator is a machine that sorts waste materials by separating flexible items from rigid ones. The machine, on an inclination, pushes light, flexible material up the screen/paddle and causes heavy, rigid items to fall downwards.
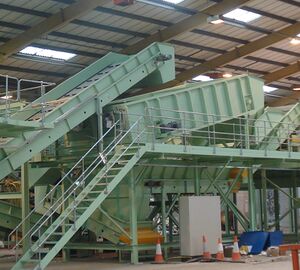
Ballistic Separator[1]
Overview
A Ballistic Separator is a machine that sorts waste materials by separating flexible items from rigid ones. The machine, on an inclination, pushes light, flexible material up the screen/paddle and causes heavy, rigid items to fall downwards. There is also small holes in the paddles where finer material can fall through and these can be sized according to customer demand. The angle of inclination and the speed of paddle rotation can be adjusted extensively. The separation characteristics can be adjusted to changes in the waste stream at any time[2].
Materials It Can Separate
This device is capable of sorting stones, glass, metal, wood, plastic, paper, containers, cans, construction and demolition waste, other heavy items, MSW and C&I waste. The separator divides the waste input into three streams: 2-dimensional light and flat material (such as paper and cardboard, 3-dimensional heavy and rigid items such as glass bottles, and fine pieces of waste[3].
Stated Advantages Over Other Separation Systems
- Easy and safe maintenance
- Versatility: enables processing of different material streams within a single system
- Ability to simply change the angle of equipment to refine sorting
- Lower operating & maintenance costs
- Constant performance with an all steel screening surface
- High throughput capacity with lower energy consumption
- Easy adaptation to different materials
- High amplitude/rotation paddle movement improves the quality of the separation[2]
The Process
Schematic Diagram of a Ballistic Separator[4] |
1. The material is fed into the Ballistic Separator, via feeding shoot, onto the rotating paddles |
2. The small pieces of waste fall/are sieved through the holes/openings in the paddles and is caught in the collecting tank for fines | |
3. The light and flat (2D) material walks/is pushed up the screens by the inclined rotating paddles and falls over the top to form the light fraction | |
4. The heavy and rigid (3D) items fall/roll down the screens and off the lower end of the machine to form the heavy fraction | |
5. The slope can be adjusted to suit the material being screened – the steeper the slope the cleaner the flat, large material and the volume of roll back increases and vice versa[5] |