Material Recovery Facility: Difference between revisions
Imported from text file |
No edit summary |
||
(26 intermediate revisions by 4 users not shown) | |||
Line 1: | Line 1: | ||
[[Category:Technologies & Solutions]] | [[Category:Technologies & Solutions]] | ||
A Material Recovery Facility is often referred to as a | A [[Material Recovery Facility]] is often referred to as a ‘[[MRF]]’ and is generically a facility that sorts, grades and prepares waste fractions suitable for onward dispatch to a [[Reprocessor]]. | ||
[[File:021 Mixed-Waste-Processing-1200x797.jpg|400px|left|Picture of Machinex DMR MRF, courtesy of Machinex, all rights reserved]]__TOC__ | |||
<br clear='left'/> | |||
==Overview== | |||
A [[Material Recovery Facility]] is often referred to as a ‘[[MRF]]’ and is generically a facility that sorts, grades and prepares waste fractions suitable for onward dispatch to a [[Reprocessor]]. Many also refer to a MRF as a Material Recycling Facility, which is not strictly true in that the MRF separates the material for onward recycling rather than recycling the material in its own right. | |||
The key elements of MRF design and operation include: | |||
* Throughput capacity - measured in both weight and volume due to differing bulk densities of materials that impact on the design of the sorting machinery, capacity of conveyors and storage areas | |||
* Reliability - the operational availability of the plant and the time required to maintain it | |||
* Quality of Outputs - high quality outputs ensure a solid, higher value market for the materials recovered | |||
* Adaptability - the ability to adjust to changing inputs over time | |||
In all of these factors, the quality of the input materials clearly has a major influence. Poor quality materials, or materials that are heavily contaminated at the input stage, can lead to lower quality outputs and/or higher levels of rejects as part of the process. | |||
==Types of MRF== | |||
There are essentially four broad types of MRF: | |||
*'''"Single-Stream" MRFs''' that are focused on one [[recyclate]] stream, removing any contamination/contrary materials from that material to produce a high quality [[recyclate]] with high value. | |||
*'''"Clean" MRFs''' that are focused on [[Dry Mixed Recyclables]] ([[DMR]]). They remove contamination/contrary materials in the input mix and produce a variety of separate good quality [[recyclate]] streams with good value, with low levels of contrary materials . | |||
*'''"Dirty" MRFs'''/'''Waste to Fuel MRF''' which extract some [[recyclate]] from mixed [[MSW]] and [[Commercial Waste]] streams with more of a focus on producing a [[Waste Derived Fuel]] ([[WDF]]). [[Recyclate]] tends to be of poor quality and of lower value. | |||
*'''Material specific MRFs''' for example: | |||
**[[Construction and Demolition Waste]] and skip wastes. | |||
**[[Waste Electrical and Electronic Equipment]] | |||
**[[Plastic]] materials and purpose designed '''[[PRF]]s''' ([[Plastics Recovery Facility]] or [[Plastics Recovery Facility | Plastics Recycling Facility]]) | |||
MRFs are increasingly using a variety of automated technologies to reduce the amount of manual sorting of materials by people. Historically simple mechanical systems have evolved, and new systems include the use of infra red and air-based systems. Current advances including moving towards robotic sorting using the latest artificial intelligence systems. | |||
=="Clean" MRFs== | |||
'''"Clean" MRFs''' accept materials from source separation schemes and [[Dry Mixed Recyclables]] ([[DMR]]). A pictorial overview of one type layout/configuration is shown below for multiple streams of [[DMR]], whereas a single stream or twin stream input would have a far more straightforward layout<ref>Suez Recycling and Recovery UK</ref>: | |||
{| | |||
|- | |||
|rowspan=7|[[File:Suez MRF drawing.png|MRF Diagram|link=[[Suez]]]]||1. Material Feed - often delivered via a [[Bag Breaker]] | |||
|- | |||
|2a.[[wikipedia:Trommel screen|Trommel Screen]] - normally used to separate off the larger, lighter mixed [[Paper & Card|paper and cardboard]] fractions from the other materials | |||
|- | |||
|2b.[[Ballistic Separator]] - normally used to separate 2-dimensional light and flat items (such as [[Paper & Card|paper and cardboard]]) from 3-dimensional heavier rigid items such as [[glass]] bottles and cans | |||
|- | |||
|3a.[[Magnetic Separator]] - used to separate [[steel cans]]/[[Ferrous Metal|ferrous metals]] | |||
|- | |||
|3b.[[wikipedia: Air knife| Air Knife]]/Air Separator - used to separate heavy from light materials, in this case to remove contamination from the [[glass]] fraction | |||
|- | |||
|4.[[Eddy Current Separator]] - used to separate [[aluminium cans]]/[[Non-Ferrous Metal|non-ferrous metals]] | |||
|- | |||
|5.[[NIR Optical Sorting]] - Near Infra Red (NIR) light is used to separate materials, often focused on different [[plastic]] types/polymers | |||
|} | |||
The [[MRF Code of Practice]] applies to all 'Qualifying MRFs' which are those all those MRFs that receive more than 1,000 tonnes per annum of primarily [[DMR]] materials from households and other sources with a similar composition. This has allowed the performance of MRFs to be compared, including the level of contamination and associated rejects from each MRF. A full list of these sites can be found on the page [[Qualifying MRFs]]. | |||
=="Dirty MRFs"== | |||
'''''content to follow''''' | |||
==Material Specific MRFs== | |||
===[[Construction and Demolition Waste]] and Skip Wastes=== | |||
'''''content to follow''''' | |||
===[[Waste Electrical and Electronic Equipment]]=== | |||
'''''content to follow''''' | |||
===[[Plastic]] Materials and Purpose Designed '''[[PRF]]s'''=== | |||
'''''content to follow''''' | |||
==References== | |||
<references /> |
Latest revision as of 11:27, 16 May 2023
A Material Recovery Facility is often referred to as a ‘MRF’ and is generically a facility that sorts, grades and prepares waste fractions suitable for onward dispatch to a Reprocessor.
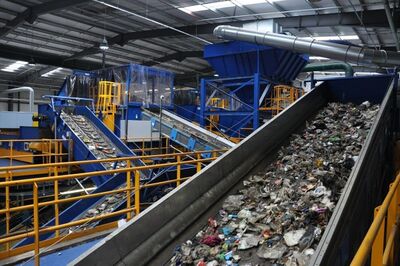
Overview
A Material Recovery Facility is often referred to as a ‘MRF’ and is generically a facility that sorts, grades and prepares waste fractions suitable for onward dispatch to a Reprocessor. Many also refer to a MRF as a Material Recycling Facility, which is not strictly true in that the MRF separates the material for onward recycling rather than recycling the material in its own right.
The key elements of MRF design and operation include:
- Throughput capacity - measured in both weight and volume due to differing bulk densities of materials that impact on the design of the sorting machinery, capacity of conveyors and storage areas
- Reliability - the operational availability of the plant and the time required to maintain it
- Quality of Outputs - high quality outputs ensure a solid, higher value market for the materials recovered
- Adaptability - the ability to adjust to changing inputs over time
In all of these factors, the quality of the input materials clearly has a major influence. Poor quality materials, or materials that are heavily contaminated at the input stage, can lead to lower quality outputs and/or higher levels of rejects as part of the process.
Types of MRF
There are essentially four broad types of MRF:
- "Single-Stream" MRFs that are focused on one recyclate stream, removing any contamination/contrary materials from that material to produce a high quality recyclate with high value.
- "Clean" MRFs that are focused on Dry Mixed Recyclables (DMR). They remove contamination/contrary materials in the input mix and produce a variety of separate good quality recyclate streams with good value, with low levels of contrary materials .
- "Dirty" MRFs/Waste to Fuel MRF which extract some recyclate from mixed MSW and Commercial Waste streams with more of a focus on producing a Waste Derived Fuel (WDF). Recyclate tends to be of poor quality and of lower value.
- Material specific MRFs for example:
- Construction and Demolition Waste and skip wastes.
- Waste Electrical and Electronic Equipment
- Plastic materials and purpose designed PRFs (Plastics Recovery Facility or Plastics Recycling Facility)
MRFs are increasingly using a variety of automated technologies to reduce the amount of manual sorting of materials by people. Historically simple mechanical systems have evolved, and new systems include the use of infra red and air-based systems. Current advances including moving towards robotic sorting using the latest artificial intelligence systems.
"Clean" MRFs
"Clean" MRFs accept materials from source separation schemes and Dry Mixed Recyclables (DMR). A pictorial overview of one type layout/configuration is shown below for multiple streams of DMR, whereas a single stream or twin stream input would have a far more straightforward layout[1]:
![]() |
1. Material Feed - often delivered via a Bag Breaker |
2a.Trommel Screen - normally used to separate off the larger, lighter mixed paper and cardboard fractions from the other materials | |
2b.Ballistic Separator - normally used to separate 2-dimensional light and flat items (such as paper and cardboard) from 3-dimensional heavier rigid items such as glass bottles and cans | |
3a.Magnetic Separator - used to separate steel cans/ferrous metals | |
3b. Air Knife/Air Separator - used to separate heavy from light materials, in this case to remove contamination from the glass fraction | |
4.Eddy Current Separator - used to separate aluminium cans/non-ferrous metals | |
5.NIR Optical Sorting - Near Infra Red (NIR) light is used to separate materials, often focused on different plastic types/polymers |
The MRF Code of Practice applies to all 'Qualifying MRFs' which are those all those MRFs that receive more than 1,000 tonnes per annum of primarily DMR materials from households and other sources with a similar composition. This has allowed the performance of MRFs to be compared, including the level of contamination and associated rejects from each MRF. A full list of these sites can be found on the page Qualifying MRFs.
"Dirty MRFs"
content to follow
Material Specific MRFs
Construction and Demolition Waste and Skip Wastes
content to follow
Waste Electrical and Electronic Equipment
content to follow
Plastic Materials and Purpose Designed PRFs
content to follow
References
- ↑ Suez Recycling and Recovery UK