NIR Optical Sorting
Near infra-red/NIR Optical Sorting systems use advanced infra-red sensors to effectively identify materials/feedstock of different wavelengths. The targeted materials are then ejected via a compressed air valve to achieve the purpose of sorting[1].
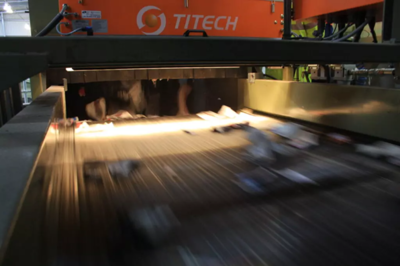
History
The first NIR sorting systems were used to process recyclable materials at the beginning of the 1990s and the technology has developed significantly in the past five to 10 years. These systems are frequently used in MRFs to streamline the sorting process, reduce labour costs, and increase the throughput to make recycling operations more efficient[2]. NIR Optical Sorting systems are capable of processing packaging, papers, waste electrical equipment, residual waste (RDF), plastics and vehicle recycling[3].
The Principle
The basic principle behind the NIR technology is measuring the wavelength of the light that bounces off an object. The conveyor in a MRF moves the material under a bright light which fires near infra-red wavelengths of light at the recyclables. Some of the wavelengths are absorbed while others are reflected by the material. The NIR sensors that are positioned in the last third of the conveyor record the characteristics of the wavelengths bounced back from the material. From there they are able to determine and target the different types of recyclables on the belt[3] and eject the selected material from the end of the conveyor via a jet of compressed air.
The Process
|
![]() NIR Optical Sorter[4] |
Near Infra-Red/NIR Optical Sorting in the Plastics Recycling Process
NIR sorting is widely used to separate plastic by NIR Optical Sorting via transmission or reflection, sometimes in a dedicated Plastics Recovery Facility. Automatic sorters interface NIR sensing with air nozzles to sort plastic items of various resin compounds/plastic polymer types. The sensors are positioned above the high-speed conveyor and detect the unique wavelength signature of the desired polymers which subsequently get directed by air jets to their specific waste streams. Contaminants become the waste output or are directed for further processing[5].