Cement Kilns: Difference between revisions
m add page specific text |
m add page specific text |
||
Line 1: | Line 1: | ||
The production of cement utilizes waste materials in two primary ways, firstly using specific [[Industrial Waste]] and [[Mining & Quarrying Waste]] (and waste from the kiln part of the process itself) as additives and replacement for traditional raw materials, and secondly as a fuel to substitute for the use of traditional fossil fuels in a cement kiln. In 2018 1,414,195 tonnes of waste was used as raw materials and fuel in the production of cement, with just over 43% of kiln thermal input replaced by [[Waste Derived Fuel]]. The five companies manufacturing cement together supplied 78% of the cement consumed in the market in 2018. <ref>[https://cement.mineralproducts.org/documents/MPA_Cement_SD_Report_2019.pdf MPA Cement Sustainability report 2019]</ref>. | The production of cement utilizes waste materials in two primary ways, firstly using specific [[Industrial Waste]] and [[Mining & Quarrying Waste]] (and waste from the kiln part of the process itself) as additives and replacement for traditional raw materials, and secondly as a fuel to substitute for the use of traditional fossil fuels in a cement kiln. In 2018 1,414,195 tonnes of waste was used as raw materials and fuel in the production of cement, with just over 43% of kiln thermal input replaced by [[Waste Derived Fuel]]. The five companies manufacturing cement together supplied 78% of the cement consumed in the market in 2018. <ref>[https://cement.mineralproducts.org/documents/MPA_Cement_SD_Report_2019.pdf MPA Cement Sustainability report 2019]</ref>. | ||
[[Category:Technologies & Solutions]] | [[Category:Technologies & Solutions]] | ||
==The Process== | ==The Process== | ||
There are six main stages of cement manufacture<ref>https://civiltoday.com/civil-engineering-materials/cement/106-cement-manufacturing-process</ref>: | There are six main stages of cement manufacture<ref>https://civiltoday.com/civil-engineering-materials/cement/106-cement-manufacturing-process</ref>: | ||
Line 10: | Line 11: | ||
* Stage 6 - '''Packing and Shipping''': the cement is conveyed from grinding mills to silos where it is then packed in bags. | * Stage 6 - '''Packing and Shipping''': the cement is conveyed from grinding mills to silos where it is then packed in bags. | ||
Not all cement kilns have have the total 'end to end' process on site, with some sites producing the clinker for subsequent grinding, blending and packing at a different site. This might include, for example, the introduction of other materials, such as Blast Furnace Slag to produce a Blast Furnace Cement - a highly sulphate resistant cement that can have up to 65% granulated Blast Furnace Slag mixed with the clinker. As Blast Furnace Slag is considered a primary input for this type of cement, it is not defined as waste and therefore is not normally captured in [[UK Waste Tonnage]]. | The introduction of waste materials - or 'Alternative Raw Materials' as coined by the industry - can be as part of the kiln phase (or Kiln Feed stage) or the final grinding stage (or Interground stage) and the percentage of recycled content of cement in 2018 is summarized in the following graphic and was almost 10% <ref>[https://cement.mineralproducts.org/documents/MPA_Cement_SD_Report_2019.pdf MPA Cement Sustainability report 2019]</ref>:see diagram below: | ||
[[File:Cement recycled content graphic.png|400px|left|Figure 2 from MPA Cement Sustainability Report, 2019]] | |||
<br clear='left'/> | |||
Not all cement kilns have have the total 'end to end' process on site, with some sites producing the clinker for subsequent grinding, blending and packing at a different site. This might include, for example, the introduction of other materials, such as Blast Furnace Slag to produce a Blast Furnace Cement - a highly sulphate resistant cement that can have up to 65% granulated Blast Furnace Slag mixed with the clinker. As Blast Furnace Slag is considered a primary input for this type of cement, it is not defined as waste and therefore is not normally captured in [[UK Waste Tonnage]]. | |||
==List of Cement Kilns== | ==List of Cement Kilns== | ||
Line 28: | Line 36: | ||
|} | |} | ||
<br clear="all" /> | <br clear="all" /> | ||
==List of Grinding and Blending Sites== | ==List of Grinding and Blending Sites== |
Revision as of 17:30, 7 April 2020
The production of cement utilizes waste materials in two primary ways, firstly using specific Industrial Waste and Mining & Quarrying Waste (and waste from the kiln part of the process itself) as additives and replacement for traditional raw materials, and secondly as a fuel to substitute for the use of traditional fossil fuels in a cement kiln. In 2018 1,414,195 tonnes of waste was used as raw materials and fuel in the production of cement, with just over 43% of kiln thermal input replaced by Waste Derived Fuel. The five companies manufacturing cement together supplied 78% of the cement consumed in the market in 2018. [1].
The Process
There are six main stages of cement manufacture[2]:
- Stage 1 - Raw Material Extraction: raw ingredients include limestone, sand and clay, shale, fly ash, mill scale and bauxite. Materials are mined, crushed and reduced in size.
- Stage 2 - Grinding, Proportioning and Blending: the production of a fine homogeneous mix with additives that comprises primarily around 80% limestone and 20% clay.
- Stage 3 - Pre-heating Raw Material: a pre-heating chamber using kiln 'exhaust' gases to reduce energy consumption and pre-condition the raw material into oxides.
- Stage 4 - Kiln Phase: the principle phase which produces a clinker, exiting the kiln in marble-sized nodules - it is the binder that is use din cement products.
- Stage 5 - Cooling and Final Grinding: the clinker is rapidly air-cooled and gypsum (and other active ingredients as required) is added to the clinker and ground to a fine power to produce cement
- Stage 6 - Packing and Shipping: the cement is conveyed from grinding mills to silos where it is then packed in bags.
The introduction of waste materials - or 'Alternative Raw Materials' as coined by the industry - can be as part of the kiln phase (or Kiln Feed stage) or the final grinding stage (or Interground stage) and the percentage of recycled content of cement in 2018 is summarized in the following graphic and was almost 10% [3]:see diagram below:
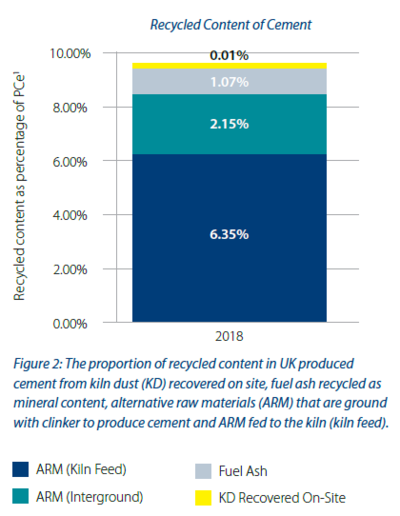
Not all cement kilns have have the total 'end to end' process on site, with some sites producing the clinker for subsequent grinding, blending and packing at a different site. This might include, for example, the introduction of other materials, such as Blast Furnace Slag to produce a Blast Furnace Cement - a highly sulphate resistant cement that can have up to 65% granulated Blast Furnace Slag mixed with the clinker. As Blast Furnace Slag is considered a primary input for this type of cement, it is not defined as waste and therefore is not normally captured in UK Waste Tonnage.
List of Cement Kilns
More detailed information can be found by clicking through to the site-specific page:

List of Grinding and Blending Sites
Site | Company | Process |
---|---|---|
Tilbury | Cemex | Grinding and Blending |
Dagenham | Breeden | Blending only |
Dewsbury | Breeden | Blending only |
Theale | Breeden | Blending only |
Walsall | Breedon | Blending only |
Barnstone | Tarmac | Grinding only |
Celtic Ash | Tarmac | Blending only |
Northfleet | Tarmac | Blending only |
Seaham | Tarmac | Blending only |
Scotash | Tarmac | Blending only |
West Thorrock | Tarmac | Blending only |
[4].